CNC Machining Services: Your Precision Engineering Partner
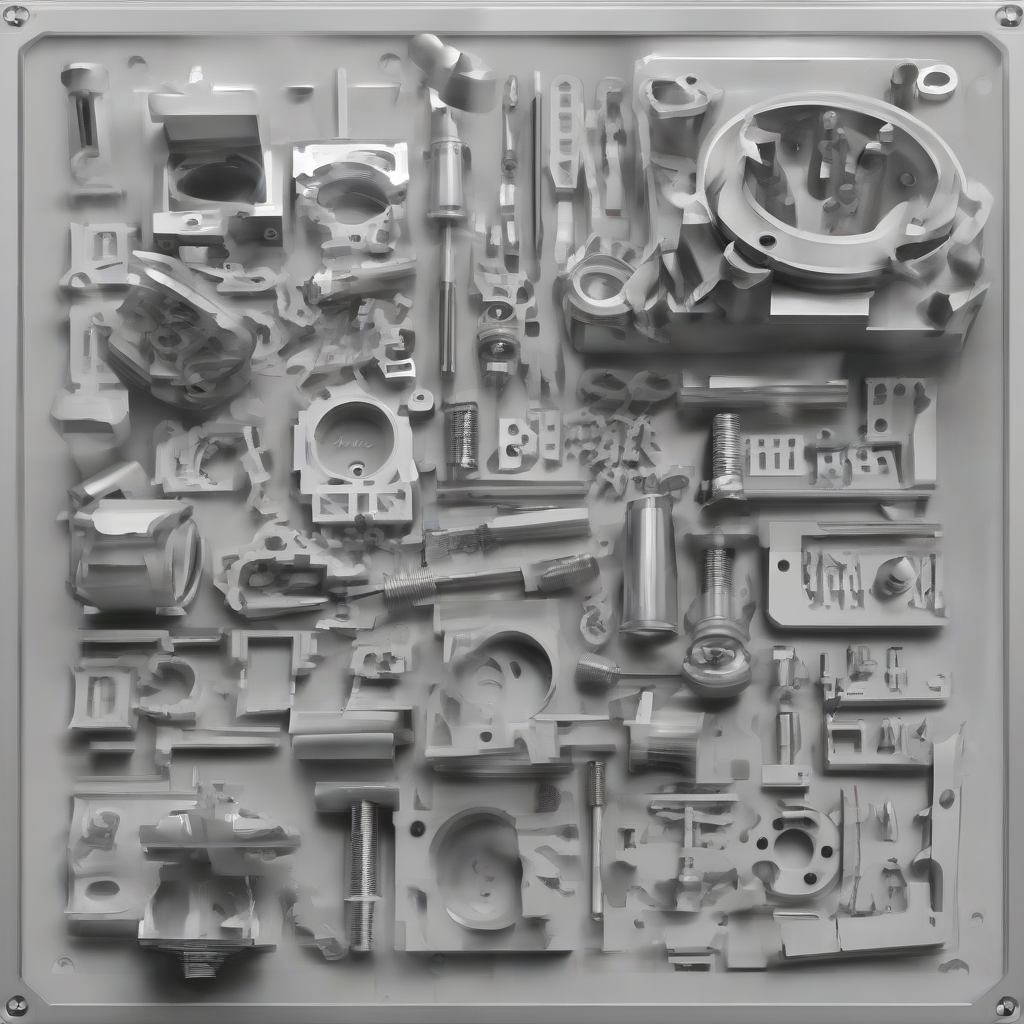
CNC Machining Services: Your Precision Engineering Partner
CNC machining, the cornerstone of modern manufacturing, offers unparalleled precision and efficiency in creating complex parts from various materials. This comprehensive guide explores the world of CNC machining services, detailing the process, applications, benefits, and considerations for businesses seeking these crucial services.
Understanding CNC Machining
Computer Numerical Control (CNC) machining utilizes computer-controlled machines to precisely manipulate cutting tools, shaping raw materials into intricate designs. Unlike traditional methods, CNC machining boasts superior accuracy, repeatability, and speed. The process typically involves:
- Design and Programming: Creating a precise 3D model of the desired part using CAD (Computer-Aided Design) software. This model is then translated into a CNC program (G-code) that instructs the machine on the necessary movements and cutting operations.
- Material Selection: Choosing the appropriate material based on the part's requirements, including strength, durability, and aesthetic considerations. Common materials include metals (aluminum, steel, titanium), plastics, and composites.
- Machine Setup: Securely fixing the raw material to the machine bed and ensuring the cutting tools are properly aligned and sharpened. This precise setup is critical for achieving accurate results.
- Machining Process: The CNC machine follows the programmed instructions, precisely moving the cutting tools to remove material and create the desired shape. Various cutting operations are possible, such as milling, turning, drilling, and engraving.
- Quality Control: Thorough inspection of the finished part to verify its dimensions, surface finish, and overall quality. This often involves measuring tools and advanced inspection techniques.
- Finishing (Optional): Further processing steps may be required, such as surface treatments (anodizing, plating), heat treatments, or other finishing techniques to enhance the part's properties.
Types of CNC Machining
Several CNC machining processes cater to diverse manufacturing needs. The most common include:
- Milling: A subtractive process that uses rotating cutters to remove material from a workpiece, creating complex shapes and features.
- Turning: A subtractive process that rotates a workpiece against a stationary cutting tool, typically used to create cylindrical or conical shapes.
- Drilling: Creating holes in a workpiece using a rotating drill bit.
- Engraving: Creating precise markings or designs on a workpiece's surface.
- Routing: Similar to milling, but often involves larger cutting tools and is suitable for larger workpieces or materials.
- Wire EDM (Electrical Discharge Machining): A non-traditional method that uses electrical sparks to erode material, ideal for intricate designs and hard-to-machine materials.
Benefits of Using CNC Machining Services
Outsourcing CNC machining offers numerous advantages for businesses:
- High Precision and Accuracy: CNC machines deliver exceptional accuracy and repeatability, resulting in parts with precise dimensions and tolerances.
- Increased Efficiency and Productivity: Automated processes significantly reduce production time compared to manual methods.
- Cost-Effectiveness: While initial investment can be substantial, outsourcing CNC machining often proves more cost-effective for smaller production runs or specialized parts.
- Complex Part Creation: CNC machining can produce parts with intricate geometries and features that would be impossible or impractical using traditional methods.
- Material Versatility: A wide range of materials can be machined, allowing for design flexibility and optimal material selection.
- Reduced Labor Costs: Outsourcing eliminates the need for hiring and training skilled machinists.
- Improved Quality Control: Reputable CNC machining services maintain rigorous quality control procedures, ensuring consistent part quality.
- Faster Turnaround Times: Many service providers offer quick turnaround times, minimizing production delays.
Choosing a CNC Machining Service Provider
Selecting the right CNC machining service provider is crucial for project success. Consider these factors:
- Experience and Expertise: Look for a provider with extensive experience in your specific industry and material requirements.
- Machining Capabilities: Ensure the provider possesses the necessary equipment and expertise to handle your project's complexity and scale.
- Quality Control Measures: Investigate the provider's quality control procedures and certifications (e.g., ISO 9001).
- Turnaround Time and Delivery: Inquire about typical turnaround times and their ability to meet your project deadlines.
- Pricing and Cost Structure: Obtain detailed quotes and compare pricing from multiple providers.
- Communication and Customer Service: A responsive and communicative provider ensures a smooth and efficient process.
- Technology and Equipment: Modern and well-maintained equipment is essential for achieving high precision and efficiency.
- Safety and Environmental Standards: Confirm the provider adheres to strict safety and environmental regulations.
Applications of CNC Machining
CNC machining finds widespread application across numerous industries, including:
- Aerospace: Manufacturing precision parts for aircraft engines, airframes, and spacecraft.
- Automotive: Producing engine components, body parts, and chassis elements.
- Medical: Creating implants, surgical instruments, and medical devices.
- Electronics: Manufacturing circuit boards, enclosures, and other components.
- Energy: Producing parts for turbines, pumps, and other energy-related equipment.
- Robotics: Creating intricate parts for robotic arms, sensors, and other robotic components.
- Consumer Goods: Manufacturing parts for appliances, electronics, and other consumer products.
Material Considerations in CNC Machining
The choice of material significantly impacts the machining process and the final product's properties. Common materials include:
- Aluminum: Lightweight, corrosion-resistant, and easily machinable.
- Steel: High strength and durability, but can be more challenging to machine.
- Titanium: High strength-to-weight ratio, excellent corrosion resistance, and biocompatibility, but difficult to machine.
- Plastics: Versatile, lightweight, and cost-effective, suitable for a wide range of applications.
- Composites: Combining the properties of different materials for enhanced performance.
Future Trends in CNC Machining
The field of CNC machining is continuously evolving, with several key trends shaping its future:
- Additive Manufacturing Integration: Combining CNC machining with additive manufacturing (3D printing) for hybrid manufacturing processes.
- Automation and Robotics: Increased automation and robotics for greater efficiency and reduced labor costs.
- Advanced Materials: Machining of advanced materials, such as ceramics and composites, for specialized applications.
- Smart Manufacturing: Integration of sensors, data analytics, and AI for improved process control and optimization.
- Improved Software and CAM Systems: More sophisticated CAM (Computer-Aided Manufacturing) software for optimized toolpaths and reduced machining time.
What's Your Reaction?

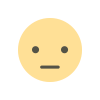
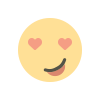
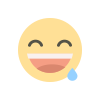
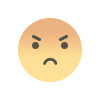
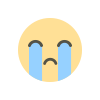
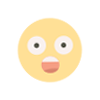